
3D-Metal Forming
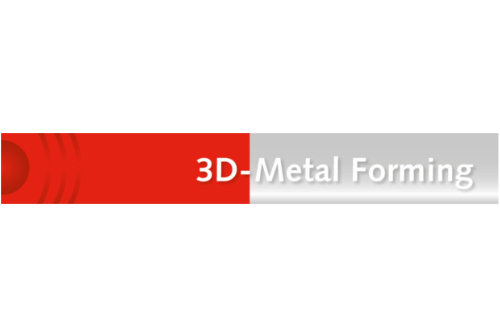
Address details:
Karperweg 8
Lelystad NL
Contact details:
Marcel Oud
T: +31 320 760 280
E: info@3dmetalforming.com
W: www.3dmetalforming.com
Segments:
- Aircraft Manufacturing
- Services
Location on the map:
**Introduction**
3D Metal Forming B.V. (tradename Exploform) specializes in the use of energetic materials for production purposes.
It all started with TNO (Dutch Research Organization) launching a research program to re-introduce forming and bonding by making use of controlled explosives. The conclusion was that Explosive forming is a valuable addition to existing metal forming technologies: unique design and manufacturing solutions can be accomplished for double curved products. In 1998 Exploform B.V. was founded by TNO Prins Maurits Laboratory followed by ISO 9001 certification in 2004. In 2005 a Joint venture between TNO and van Campen Aluminum was set up, 2010: the name changed from Exploform B.V. to 3-D Metal Forming B.V.
**Benefits Of Explosive Forming Of Integral Components**
- Controlled process and repetitive high quality output
- Lowest product weight due to optimized design and no rivets etc.
- Lowest part count, no assembly needed
- Simple Supply Chain resulting in lower cost, easy production planning, shorter throughput time
- Excellent impact resistance
- Lowest integral cost
**Targeted Markets**
- Aerospace: integral double curved airframe and engine components, bonding (unweldable) metals
- Energy: special purpose (double curved) equipment for nuclear & steam application ; bonding (unweldable) metals
- Building/Construction: cladding
**Production Capabilities**
Our core production capabilities are:
- Forming of large and complex (double curved) components out of sheet or plate material. Starting of plate dimension can be as large as 3 m. by 5 m. with a thickness of approximately 150 mm. Example applications are: integral cockpit structures, bulkheads, nose lips, transition pieces and lobe mixers.
- Bonding of different materials ie. bonding a Titanium layer to Aluminum structural components for connecting Composite materials, bonding of Molybdenum and Copper.
**Engineering Capabilities**
We have invested heavily in engineering capabilities for providing optimal support to our customers in developing new products.
We are highly experienced in 3D CAD and CADCAM operations and we have FEM simulation software (Autoform, ANSYS/Autodyn) for simulating our processes. Furthermore we are experienced in analyzing shapes and deformations with our photogrammetry system. This enables us to advise in developing new products and predict the product properties (e.g. thickness, remaining elongation of the metal) during and after forming.